Top 10 Industrial Automation & Control Trends – Convergence, Divergence, or Chaos?
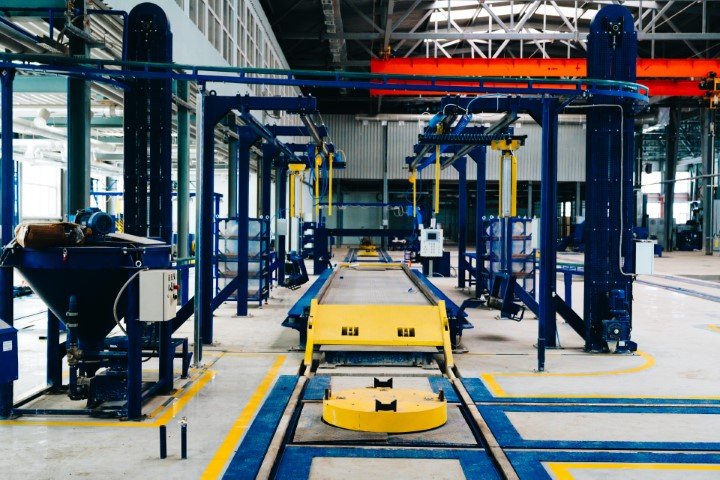
2016 was an exciting year of innovation and exploration in industrial automation. While the calendar year has now changed, the buzz throughout the industry has not. Major control industry suppliers are refining their longstanding offerings with the new technologies and, more importantly, nontraditional suppliers are entering the fray, leveraging the technological and IoT advancements to introduce new and different products. All this cutting-edge development further fuels the excitement, but also begs a relevant question:
Will these developments lead to convergence, divergence, and/or chaos in 2017 and beyond?
I’ve been involved in this industry for years, as both a designer and applier of automation and controls in the field, and I still don’t know what the future will hold. Still, after a busy 2016 talking to a wide range of users, suppliers and industry consultants, while attending over 20 industry conferences and related events, I have many educated insights on the trends that will shape automation in 2017. This article will discuss ten of the most influential trends I see playing a prominent role in the industry this year. I invite everyone share their own thoughts, criticisms and perspectives on this exciting time for automation.
1. Internet of Things (IoT) Technology Will Cut Automation Costs
The discussions surrounding Internet of Things (IoT) concepts, and the technology impacting the industry, are becoming more intense. The ongoing developments of technology and products is driving the Internet of Things with connected innovations including higher-performance processors, sensors, analytic software, vision systems, cloud computing, new communications (wireless & protocols) and highly distributed system architectures, among many other products. This, logically, should lead to lower cost and higher performance industrial automation systems, and will continue to expand the options to design lower cost and higher
2. Leaner & Flatter Architecture Will Come to Automation
As I have forecasted in past trends articles, the evolution to streamlined 2-3 layer automation systems is starting to occur, increasing performance and lowering future software maintenance costs. This is a significant simplification of the five layer system model (typically expressed in the 5 level Purdue model) that the automation industry has been centered on for years. This trend is accelerating, with computing being driven down into more capable controllers, intelligent devices & sensors, and driven up to plant level computers and cloud hosted applications.
3. Open Industrial Automation Architectures Will Simplify Integration
2016 saw the emergence of open industrial system architectures, with key themes centering on computing at the edge, multivendor interoperable open systems, and tight integration with business systems. Older industrial automation architectures are currently not completely open but have communities of gated ecosystems, which presents an obstacle for multi-vendor integration. This new ‘open’ way of thinking, along with the application of advanced technology, is intended to create more responsive, efficient, and flexible manufacturing that tightly integrate ecosystems of customers, suppliers, manufacturers, and distribution logistics. Achieving these goals requires frictionless communications and interaction between enterprise systems, manufacturing field I/O (inputs/outputs) including sensors, actuators, analyzers, drives, vision, video, and robotics to achieve increased manufacturing performance and flexibly. Creating superior integrated industrial automation systems in this environment requires fully open source communications, contextual data definitions & frameworks, and application interchange standards. These are some of the prominent recent initiatives: Industry 4.0, Industry 4.0 for Process, The Open Process Automation Forum
4. Vendors Must Embrace Portable Applications
One of the most challenging issues facing the automation industry, is the lack of multivendor portability of applications and this must change. The drivers behind open automation architecture initiatives recognize that without open ecosystems, providing portable applications between vendor platforms, innovation is stifled. Nontraditional suppliers are already demonstrating and selling products that are programmed with IoT software.
5. Operational Technology (OT) & Information Technology (IT) Merge
The progressively tightening integration of Operational Technology (OT) and Information Technology (IT) continues to grow, as business systems are evolving to handle real-time transaction processing, satisfying requirements for real-time synchronized manufacturing operations. Innovative vendors are already providing building blocks designed to accomplish the vision of the connected enterprise. 2016 saw several new, powerful automation controllers, which directly communicate with enterprise business systems using OPC UA Web services and other IoT transport mechanisms, that are already becoming part of the business information loop. There are a number of industry standards that are being leveraged to accomplish this including OPC UA, B2MML, PLCopen OPC UA, and IT database interfaces. These functional changes may minimize the need to have Manufacturing Execution Systems (MES) in many applications
6. Edge Devices Will Flourish
The rapid rise of Internet of Things concepts and technologies, including high power/low cost processing and communications technologies, is enabling new intelligent nodes, which operate at the network edge to improve manufacturing performance and efficiency. This will be a growing trend.
7. Democratizing Analytics and Edge/Cloud Historians Boost Big Data
Driven by a wide range of IoT implementations, outside of industrial automation, significant developments have brought users a new generation of cloud services and tools to create analytics. Previously, much of the software used to accomplish advanced process control (APC), optimization, and predictive analytics has been difficult to use and expensive, but this is changing. Driven by a wide range of Internet of Things applications, these cloud-based tools, with refined integrated design environments, provide platforms for users and industry experts to create and deploy economical analytics. These platforms significantly lower the cost of implementation and help broaden the range of applications where analytics can be applied, very similar to how Excel spreadsheets empowered users to use computers more effectively. In addition to improving efficiency and productivity, more analytics can substantially better inform decision-making in order to improve and refine manufacturing processes.
Data historians have proven their value in the process industries, and now in discrete applications as well, but the biggest limiting factors have been the initial costs and ongoing lifecycle software maintenance. The use of the commercial cloud services is providing an economical means for many companies to leverage historic data and apply analytics where appropriate. I have talked with a number of major users that are collecting plant data, using OPC, OPC UA, and other gateways, and are delivering the data to standard cloud applications from providers such as Amazon Web Services (AWS) and Microsoft Azure cloud services. They are finding this approach efficient and highly flexible.
8. Smart Sensors Will Be Everywhere
“Plug and play” smart sensors and control devices, which use embedded intelligence and do not require external software, have been proven to provide benefits (HART being a recent open architecture example) by providing increasing amounts of contextual data. The cost of implementing smart sensors has dropped dramatically, with most recent IO-Link addition that is gaining rapid adoption. There are also Ethernet sensors, that communicate using industrial and related protocols, which provide data for automation and communicate directly with business systems. Interestingly, I have been seeing Bluetooth sensors, typically found in commercial applications, being used in industrial applications, as well.
9. Wireless Networks Will Be the (Cheaper) Standard
IoT developments like these may also be the driving factor that lowers the cost of wireless sensors, which had been limiting the number of applications deployed. The installation of wireless points is still in its infancy, considering that they are still dwarfed by the number of hardwired devices being installed today. The prominent industrial wireless standards today include ISA100.11, IEC62591 (WirelessHART), IEC62601 (WIA-PA developed in China), ZigBee, and 802.11.
10. Collaborative Robots Will Become More Affordable
The number of collaborative robots exploded in 2016, as it has in multiple years before last, and my discussions with vendors indicate unit sales growth is high. These new breeds of light and inexpensive robots are designed to work cooperatively with people and integrate vision systems along with advanced software to provide situational awareness. These robots have average prices which have dropped significantly under $40,000, making them suitable for a much very larger number of applications. This breed of robots is following a similar pattern that ignited the personal computer revolution - providing a product with less power than larger offerings, but adds value for a broader number of users. The rate of robot adoption is accelerating throughout the world, which has been particularly interesting as China is now the largest purchaser of robots in the world.
The worldwide number of domestic household robots is forecasted to be 31 million between 2016 and 2019. These forecasts are takes from the 2016 World Robotics Report, "Service Robots", published by the International Federation of Robotics (IFR). This should drive the price of robots lower with increased unit volume.
Bottom Line - Big Competitive Risk. Bigger Opportunity
As these automation and control trends evolve, users and automation suppliers are faced with both risk and opportunity. The first risk is adopting these technologies before they are proven and suffering through the resulting growing pains. Not adopting these new technologies at the point of stability, companies are at risk of competitors leveraging technology to be more responsive and efficient to their consumers’ needs, taking business away or even crippling your company in the marketplace. The challenge with these major shifts in technology is that it is difficult to determine what is valuable and when to invest. Companies that are able to embrace these transformational changes at the opportune time will outpace the competition and thrive.