The Rise Of Digital Twin Technology
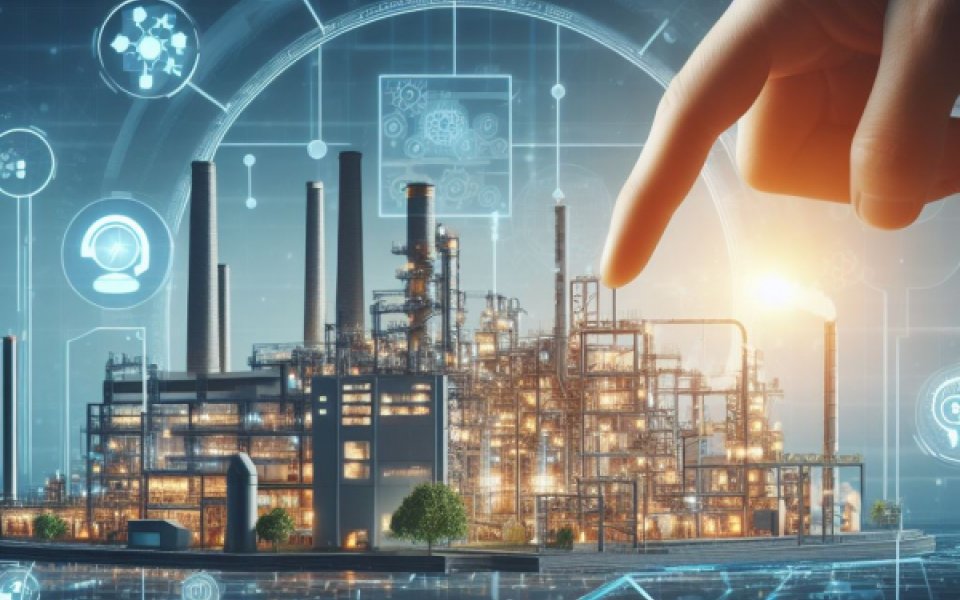
The ongoing global digital transformation is fueling innovation in all industries. One such innovation is called digital twin technology, which was originally invented 40 years ago. When the Apollo mission was developed, scientists at NASA created a digital twin of the mission Apollo and conducted experiments on the clone before the mission started. Digital twin technology is now becoming very popular in the manufacturing and healthcare industries. Did you know that the densely populated city of Shanghai has its own fully deployed digital twin (virtual clone) covering more than 4,000 kilometers? This was created by mapping every physical device to a new virtual world and applying artificial intelligence, machine learning and IoT technologies to that map. Similarly, Singapore is bracing for a full deployment of its own digital twin. The McLaren sports car already has its own digital twin. Companies like Siemens, Philips, IBM, Cisco, Bosch and Microsoft are already miles ahead in this technology, fueling the Fourth Industrial Revolution. The conglomeration of AI, IoT and data analytics predicts the future performance of a product even before the product’s final design is approved. Organizations can create a planned process using digital twin technology. With a digital twin, process failures can be analyzed ahead of production. Engineering teams can perform scenario-based testing to predict the failures, identify risks and apply mitigation in simulation labs. Digital twins produce a digital thread that can then enable data flows and provide an integrated view of asset data. These digital threads are the key to the product life cycle and help optimize product life cycles. The simulation of a digital thread can identify gaps in operational efficiencies and produce a wealth of process improvement opportunities through the application of AI. Another reason behind the overwhelming success of digital twin technology is its use in issue identification and minor product design corrections while products are in operation. For example, for a high-rise building, with a digital twin, we can identify minor structural issues and implement them in the virtual world before carrying them over to the real world, cutting down long testing cycles. By the end of this decade, scientists may come up with a fully functional digital twin of a human being that can tremendously help in medical research. There may be a digital version of some of us walking around, and when needed, it can provide updates to our family or healthcare providers regarding any critical health conditions we may have. Some powerful use cases for the use of digital twin humans include drug testing and proactive injury prevention. Organizations starting to think about implementing digital twin technology in product manufacturing should first look at the tremendous innovation done by leaders like Siemens and GE. There are hundreds of case studies published by these two organizations that are openly available on the market. The next step is to create a core research team and estimate the cost of implementing this technology with the right ROI justification for your business stakeholder. This technology is hard to implement, and it’s also hard to maintain. That’s why you should develop a long-term sustainable strategy for digital twin implementation.